Alcast Company Things To Know Before You Get This
Alcast Company Things To Know Before You Get This
Blog Article
Getting The Alcast Company To Work
Table of ContentsAll About Alcast CompanyThe 7-Second Trick For Alcast CompanyAll about Alcast CompanyThe Best Strategy To Use For Alcast CompanyWhat Does Alcast Company Do?Unknown Facts About Alcast Company
The subtle distinction lies in the chemical web content. Chemical Contrast of Cast Light weight aluminum Alloys Silicon promotes castability by reducing the alloy's melting temperature level and improving fluidity throughout spreading. It plays a critical duty in enabling elaborate mold and mildews to be filled up accurately. Furthermore, silicon adds to the alloy's stamina and put on resistance, making it important in applications where toughness is essential, such as automobile parts and engine components.It likewise enhances the machinability of the alloy, making it easier to process into ended up products. In this means, iron adds to the overall workability of light weight aluminum alloys. Copper increases electric conductivity, making it useful in electrical applications. It likewise enhances rust resistance and includes to the alloy's overall stamina.
Manganese adds to the stamina of aluminum alloys and boosts workability (aluminum foundry). It is generally utilized in wrought aluminum products like sheets, extrusions, and profiles. The existence of manganese help in the alloy's formability and resistance to fracturing throughout construction procedures. Magnesium is a lightweight aspect that offers strength and impact resistance to light weight aluminum alloys.
The 8-Second Trick For Alcast Company
Zinc boosts the castability of light weight aluminum alloys and helps manage the solidification procedure during spreading. It boosts the alloy's toughness and solidity.
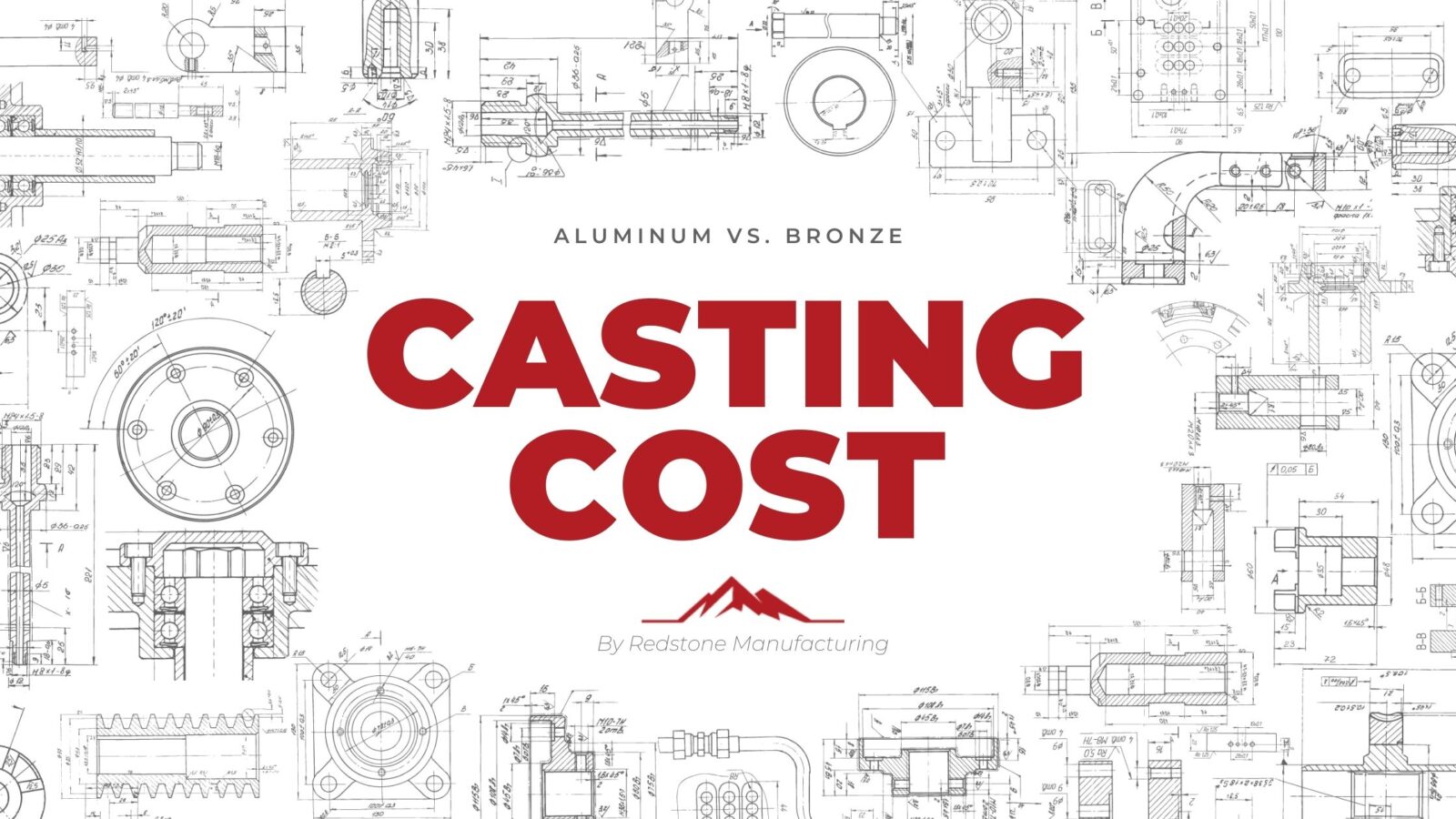
The primary thermal conductivity, tensile stamina, return toughness, and elongation vary. Select ideal raw products according to the efficiency of the target item created. Among the above alloys, A356 has the highest thermal conductivity, and A380 and ADC12 have the most affordable. The tensile limit is the opposite. A360 has the most effective return toughness and the highest prolongation rate.
What Does Alcast Company Mean?

In precision casting, 6063 is appropriate for applications where intricate geometries and high-grade surface finishes are vital. Instances include telecommunication rooms, where the alloy's premium formability permits sleek and cosmetically pleasing styles while preserving architectural integrity. In the Illumination Solutions sector, precision-cast 6063 components produce classy and reliable lighting fixtures that require elaborate forms and good thermal performance.
The A360 shows superior elongation, making it excellent for complex and thin-walled parts. In accuracy spreading applications, A360 is appropriate for sectors such as Customer Electronics, Telecommunication, and Power Tools.
6 Simple Techniques For Alcast Company
Its special properties make A360 a useful choice for accuracy spreading in these industries, enhancing product toughness and quality. Aluminum Castings. Aluminum alloy 380, or A380, is a commonly utilized spreading alloy with a number of distinct attributes.
In precision casting, light weight aluminum 413 beams in the Consumer Electronic Devices and Power Tools sectors. This alloy's premium rust resistance makes it an excellent selection for exterior applications, making sure resilient, long lasting items in the stated sectors.
Not known Details About Alcast Company
As soon as you have made a decision that the aluminum die casting procedure is ideal for your project, an important following action is picking one of the most suitable alloy. The aluminum alloy you select will significantly impact both the spreading process and the properties of the final product. As a result of this, you should make your decision very carefully and take an enlightened approach.
Identifying one of the most ideal aluminum alloy for your application will certainly imply weighing a broad array of features. These relative alloy features follow the North American Pass Away Casting Association's guidelines, and we've separated them right into 2 classifications. The very first group addresses alloy qualities that influence the manufacturing process. The second covers features influencing the residential properties of the end product.
Top Guidelines Of Alcast Company
The alloy you select for die spreading directly affects a number of elements of the casting process, like just how very easy the alloy is to collaborate with and if it is susceptible to casting defects. Hot breaking, additionally called solidification cracking, is a regular die spreading issue for aluminum alloys that can result in inner or surface-level splits or cracks.
Particular aluminum alloys are more prone to hot cracking than others, and your selection should consider this. One more common problem found in the die casting of aluminum is die soldering, which is when the cast sticks to the die walls and makes visite site ejection difficult. It can harm both the cast and the die, so you must seek alloys with high anti-soldering properties.
Rust resistance, which is already a significant quality of light weight aluminum, can differ considerably from alloy to alloy and is a crucial characteristic to consider depending on the ecological conditions your product will be exposed to (Casting Foundry). Wear resistance is one more home typically looked for in light weight aluminum items and can separate some alloys
Report this page